
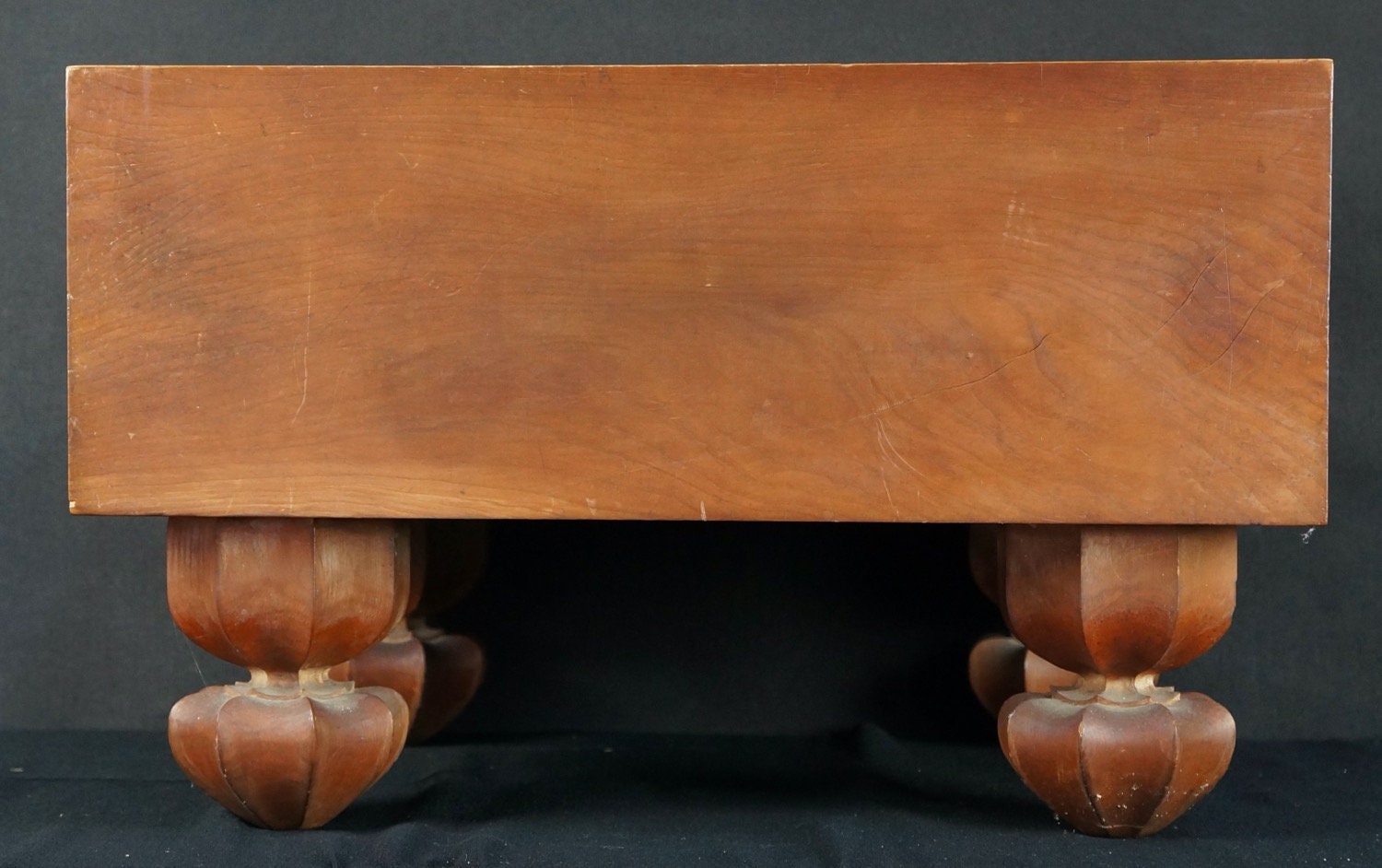
The wet slurry gypsum mix is then sandwiched between two heavy sheets of paper and kiln dried to make the board rigid. Just enough water is added to create mixture of the right consistency. Other trace ingredients might be added to the mix at this point depending on the nature of board required. Manufacturing gypsum board begins with the process of grinding and mixing the Gypsum with starch to help with bonding. In addition to this natural form, a synthetic form of gypsum is produced as a byproduct of coal-fired power plants. Gypsum is found and mined across the world with large deposits found in various countries. Even once all the water has been released from its core, gypsum board continues to serve as a heat-insulating barrier.
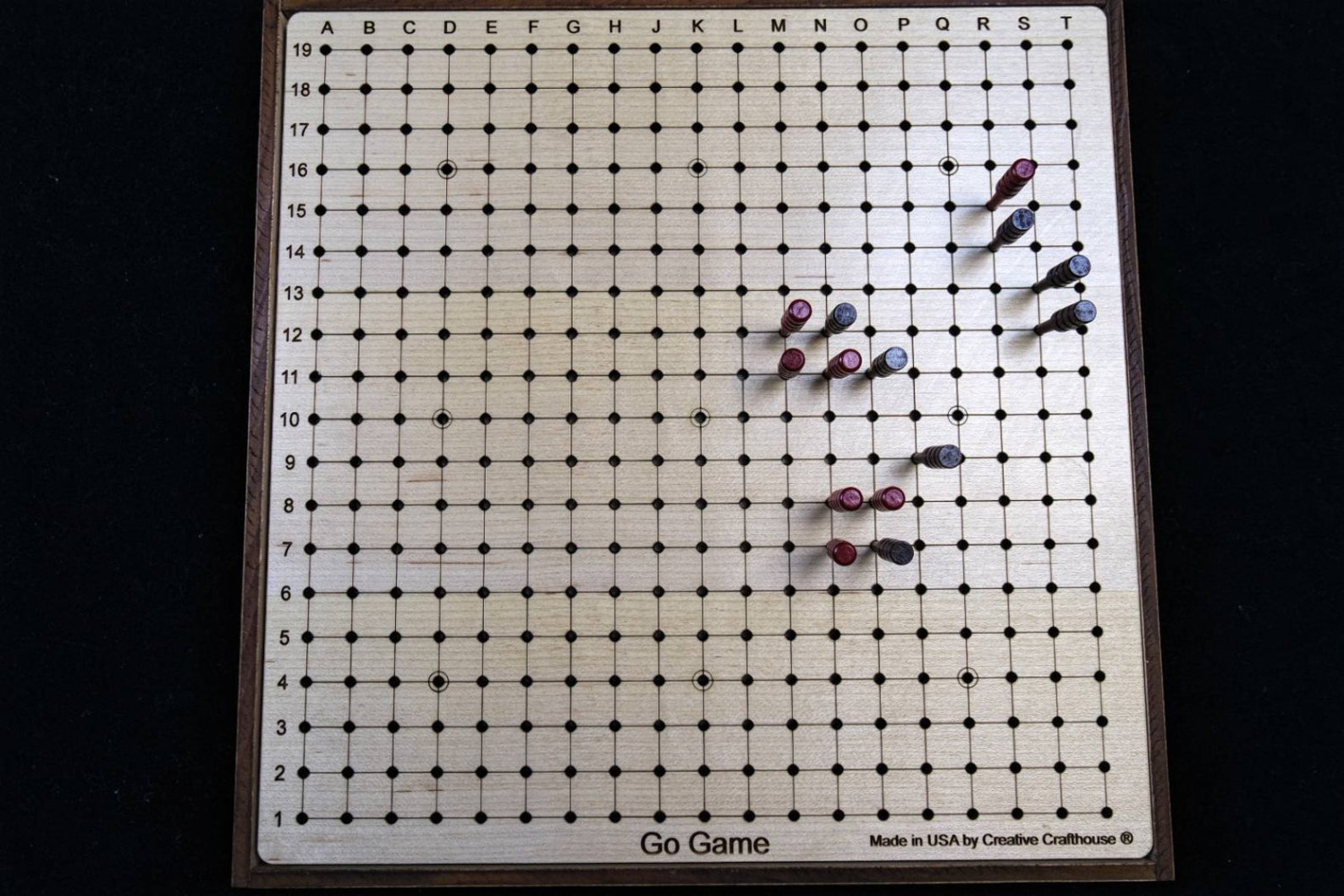
Steam does not exceed 100 degrees C under normal atmospheric pressure it therefore is very effective minimizing the transfer of heat and the spread of fire. Its non-combustible core contains nearly 21% chemically combined water, which, under high heat, slowly escapes as steam. Where fire resistance classifications are required, the use of Gypsum board offers the ideal solution. Gypsum board is an excellent fire-resistant building material. Gypsum Board Has A High Fire Resistance Level The panels consist of a mineral gypsum, or hydrous calcium sulfate with its main ingredient in plaster of paris, as well as a component of cement. In the case of Gypsum Board, used for ceilings, the boards would also be attached to the wooden ceiling beams with screws or nails and finished off. This is also known as drywall partitioning.
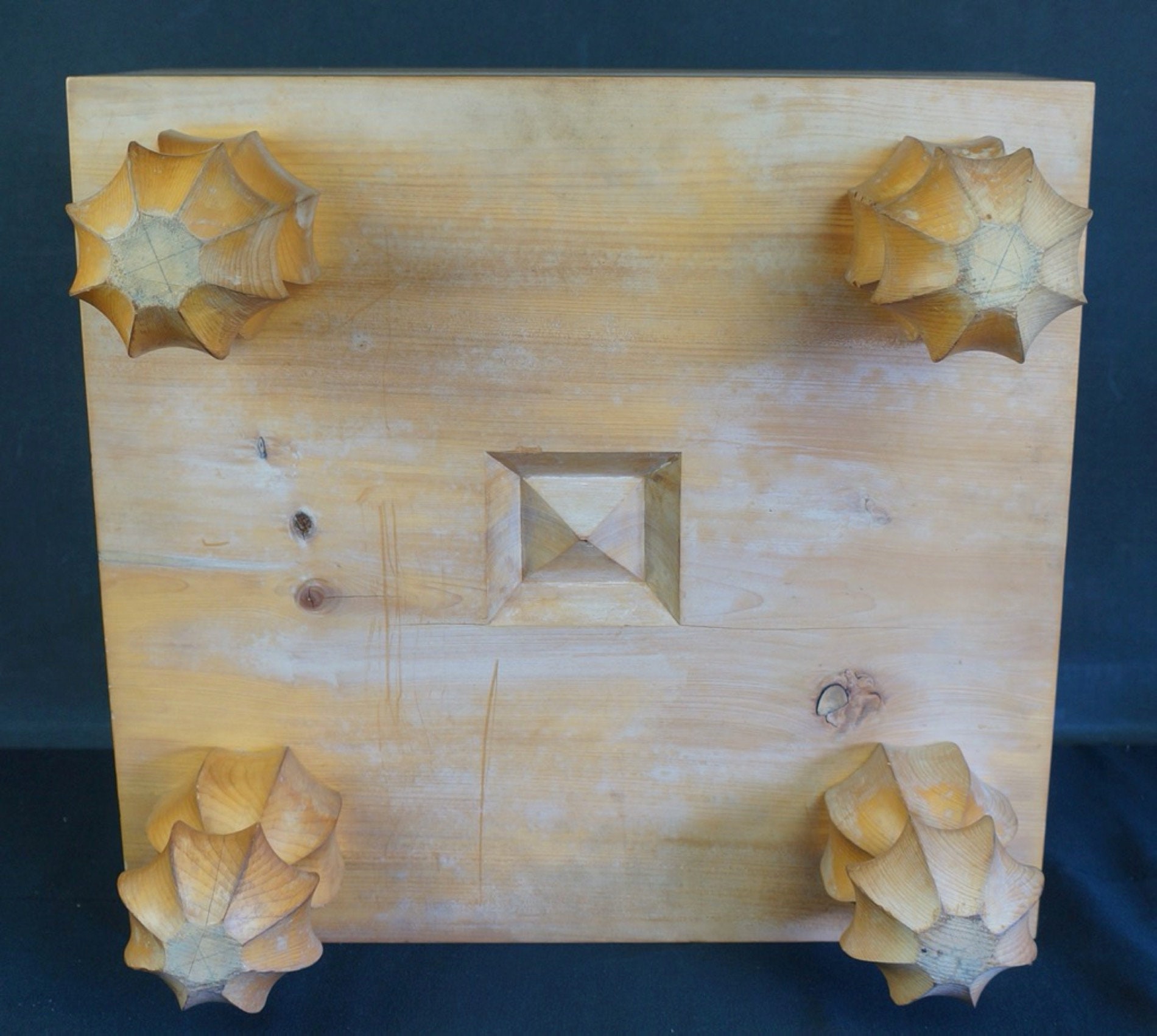
These sheets are attached to the framing by either screws or nails, and finally joined together using a specific tape and compound which leaves an even and smooth crease less surface that is finished off with a coat of paint. Vertical aluminum structures or frames are used as the skeletal structure that provides support for these sheets of gypsum board.
